齒輪泵因結(jié)構(gòu)簡單、易加工、自吸能力強(qiáng)以及對油液污染不敏感等優(yōu)點(diǎn)而被廣泛應(yīng)用于船舶、機(jī)床、國防、采礦、汽車、冶金等[1]領(lǐng)域。目前,國內(nèi)外已開展了齒輪泵間隙[2]、泵體結(jié)構(gòu)[3]、軸向間隙補(bǔ)償[4]、徑向壓力平衡、自吸性能[5]、浮動軸套結(jié)構(gòu)設(shè)計(jì)、高轉(zhuǎn)速齒輪泵主動供油系統(tǒng)以及關(guān)于液壓系統(tǒng)的氣蝕問題及預(yù)防措施[6]等方面的研究。結(jié)果發(fā)現(xiàn):齒輪泵轉(zhuǎn)速越高,其吸油腔真空度越高,自吸性能越好,但隨著齒輪泵轉(zhuǎn)速進(jìn)一步提高,由于齒廓間油液的離心運(yùn)動,齒輪泵會產(chǎn)生一定的吸空現(xiàn)象,導(dǎo)致油液內(nèi)部溶解的氣體析出從而產(chǎn)生氣穴現(xiàn)象。研究人員雖已對齒輪泵的真空度以及過度真空產(chǎn)生氣穴的情況進(jìn)行了研究,也為消除齒輪泵高轉(zhuǎn)速工況下產(chǎn)生氣穴提出了主動供油系統(tǒng)的解決方案,但對因主動供油系統(tǒng)產(chǎn)生的壓力對齒輪泵軸封的可靠性沒有很好的解決方案,基本上從提高軸封的耐壓能力予以著手,有些耐壓油封的耐壓值達(dá)到了10MPa以上,但因其工作原理導(dǎo)致在高轉(zhuǎn)速工況下極易磨損失效產(chǎn)生故障,從而影響主機(jī)的可靠性和齒輪泵的使用壽命。本文以外嚙合齒輪泵為研究對象,闡述了齒輪泵結(jié)構(gòu)特征及其工作原理,分析了齒輪泵自吸和主動供油系統(tǒng)工況之間的不同關(guān)系,并結(jié)合實(shí)際生產(chǎn)中經(jīng)驗(yàn)積累實(shí)現(xiàn)了多種優(yōu)化方法的分析和應(yīng)用。本文為應(yīng)用于一種主動供油系統(tǒng)的進(jìn)油正壓、高轉(zhuǎn)速、寬溫域高壓力輸出雙聯(lián)齒輪泵的優(yōu)化設(shè)計(jì)。
氣穴是指流動的油液在局部位置壓力下降(流速高或者壓力低真空)達(dá)到飽和蒸氣壓或空氣分離壓時(shí),產(chǎn)生空氣的分離而形成大量氣泡的現(xiàn)象。當(dāng)再次從局部低壓流向高壓區(qū)時(shí),氣泡破裂消失,在破裂消失過程產(chǎn)生局部高壓和高溫,出現(xiàn)振動和發(fā)出不規(guī)則的噪聲,金屬表面被氧化剝蝕,這種現(xiàn)象叫氣穴,又叫氣蝕。氣穴現(xiàn)象的產(chǎn)生對主機(jī)系統(tǒng)有極其嚴(yán)重的危害性,因而必須予以采取相應(yīng)的預(yù)防措施。
某些主機(jī)系統(tǒng)由于內(nèi)部空間狹小,必須通過提高齒輪泵的工作轉(zhuǎn)速以達(dá)到系統(tǒng)流量需求。由于高轉(zhuǎn)速齒輪泵容易形成吸空,導(dǎo)致氣穴現(xiàn)象發(fā)生。因而,在此類主機(jī)系統(tǒng)中均采用主動正壓供油系統(tǒng),為了保持供油的穩(wěn)定性,一般設(shè)置一定的供油壓力以保證齒輪泵的進(jìn)油腔無低壓真空現(xiàn)象的產(chǎn)生。主動供油系統(tǒng)原理如圖1所示。
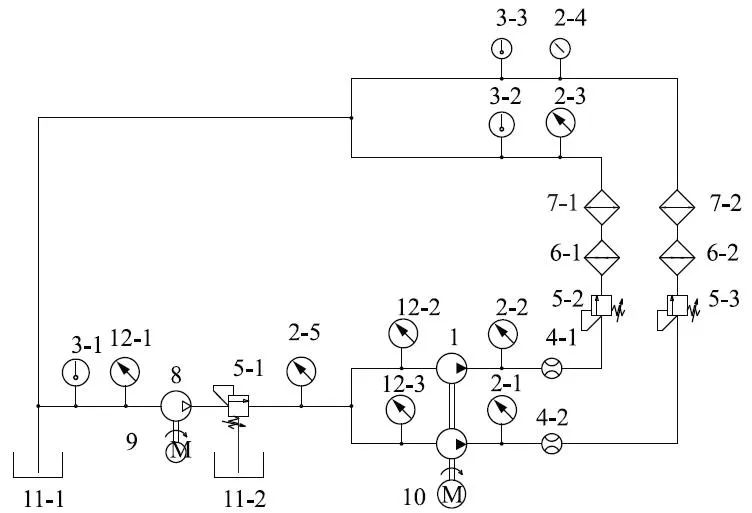
1.雙向結(jié)構(gòu)雙聯(lián)泵(小排量)3-1、3-2、3-3.溫度計(jì) 4-1、4-2.流量計(jì)5-1、5-2、5-3.溢流閥 6-1、6-2.加熱器 7-1、7-2.散熱8.増壓補(bǔ)油泵(大排量) 11-1、11-2.油箱 12-1、12-2、12-3.真空表主動供油系統(tǒng)中,工作泵為小排量高轉(zhuǎn)速齒輪泵,其進(jìn)油口和增壓補(bǔ)油泵出油口相連通,齒輪泵的旋轉(zhuǎn)軸封處始終承受系統(tǒng)設(shè)定的補(bǔ)油壓力,一般為2.5MPa左右。而且根據(jù)旋轉(zhuǎn)油封的使用特性,在高壓工況下,其允許運(yùn)行轉(zhuǎn)速將大幅下降。齒輪泵旋轉(zhuǎn)油封裝配位置典型結(jié)構(gòu)如圖2所示。
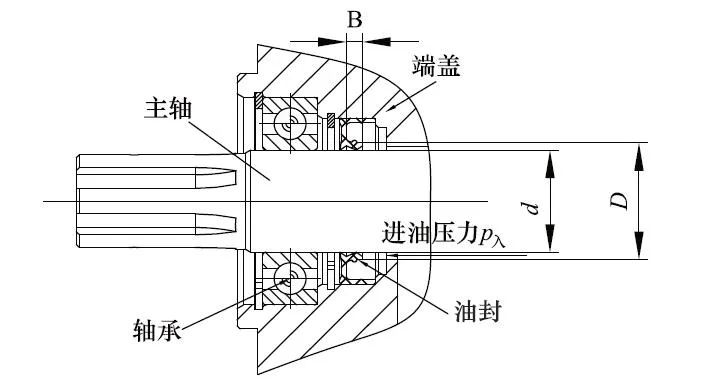
由圖2所示可知,齒輪泵軸伸直徑d,其工作轉(zhuǎn)速為n,油封唇口承壓環(huán)帶直徑為D,寬度為B,如果設(shè)定主軸和油封唇口的摩擦系數(shù)為μ,油封唇口處油壓為p入,設(shè)定此處油封唇口彈簧力為F彈,唇口橡膠變形張力為F張,則可以得出此處摩擦副所受延徑向的總法向力為:根據(jù)上述公式,我們可以得出影響油封唇口摩擦力的要素主要有三個方面,一是由軸頸粗糙度和油封唇口材料之間形成的摩擦副對應(yīng)的摩擦系數(shù)μ,二是油封設(shè)計(jì)形成彈簧力F彈和橡膠變形張力為F張以及唇口結(jié)構(gòu)π×D×B承壓環(huán)帶面積,三是油封唇口處的油液輸入壓力p入。常規(guī)齒輪泵在油封唇口處由于齒輪泵的自吸形成真空,因而油封唇口一般在結(jié)構(gòu)上設(shè)置彈簧和一定的壓縮量使其緊密貼合齒輪軸伸,此處油壓一般為負(fù)值,可以忽略。因而油封唇口所受壓力為唇口彈簧力和橡膠壓縮變形張力之和。即:在主動供油系統(tǒng)中,由于供油壓力的存在,油封唇口處F總因存在p入而大幅增加,在高轉(zhuǎn)速工況下,此處產(chǎn)生大量的摩擦熱能。其計(jì)算公式如下: 實(shí)際工況中,因供油壓力的存在,F總大幅增加,由于高轉(zhuǎn)速應(yīng)用工況的需求,行程s值較常規(guī)齒輪泵大,因而在唇口將產(chǎn)生大量摩擦熱能。由于供油壓力的存在,油封唇口處的油液不能因齒輪泵自吸返回進(jìn)油口,此處的熱量無法有效帶走產(chǎn)生高溫,從而導(dǎo)致油封唇口老化(見圖3)密封失效以及燒軸(見圖4)等故障的發(fā)生,產(chǎn)品故障率高,使用壽命短。
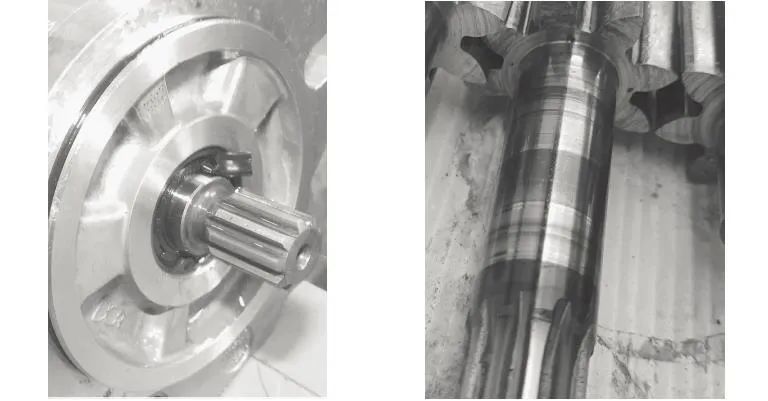
常規(guī)齒輪泵因結(jié)構(gòu)適應(yīng)性以及內(nèi)部參數(shù)設(shè)計(jì)強(qiáng)度不足等問題,在實(shí)際使用中已經(jīng)出現(xiàn)了螺栓斷裂(見圖5),軸套燒蝕(見圖6),雙聯(lián)齒輪泵連接套磨損(見圖7),容積效率下降過快等多種故障。為了提高齒輪泵的應(yīng)用前景,要求齒輪泵需具有向?qū)挏赜颍?43℃~150℃)高功率密度(高壓、高速、小型化)方向發(fā)展的能力。
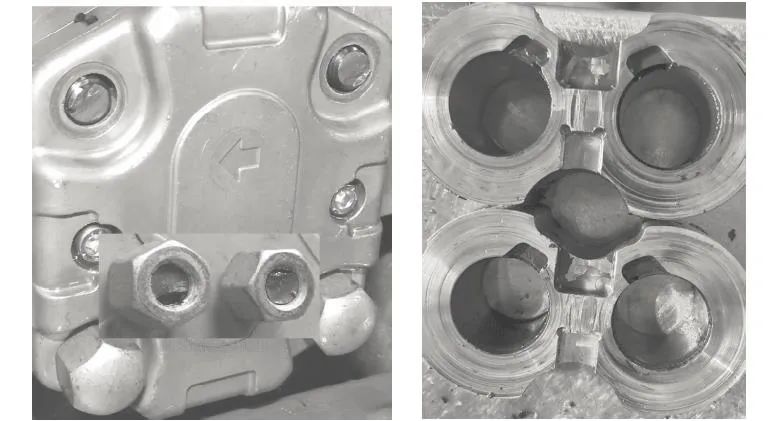
如圖3~圖5,產(chǎn)品在工作過程將產(chǎn)生軸封漏油、片間漏油以及不建壓等影響主機(jī)使用性能或者直接造成停機(jī)等嚴(yán)重故障,圖6、圖7由于承載能力不足產(chǎn)生微動磨損影響產(chǎn)品使用壽命和可靠性。為了有效解決上述故障現(xiàn)象,提高產(chǎn)品的承載能力和使用壽命,滿足特殊工況的可靠性需求,我們從產(chǎn)品結(jié)構(gòu),齒輪參數(shù),材料應(yīng)用等多方面予以分析解決。
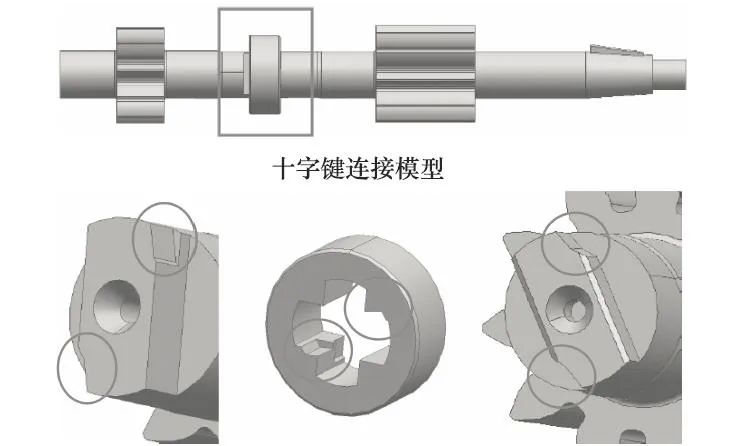
2.1 軸套采用雙向密封結(jié)構(gòu)設(shè)計(jì)解決齒輪泵進(jìn)油腔道正壓油封不承受高壓問題
常規(guī)齒輪泵浮動軸套內(nèi)部密封采用高、低壓區(qū)分開,單旋轉(zhuǎn)方向的密封方式,其進(jìn)油口的壓力不允許高于0.3MPa。對于齒輪泵進(jìn)油腔道正壓供油,當(dāng)齒輪泵進(jìn)油口壓力為2.5MPa,這就需要油封的耐壓大于2.5MPa至3MPa以上,這種方案由于進(jìn)油腔道通過軸套背面回油槽處和旋轉(zhuǎn)密封腔道的接通(見圖8)。因而,進(jìn)油腔道的壓力和壓力波動將直接傳遞到旋轉(zhuǎn)油封處,對油封的要求較高,在高溫、高壓、高速的情況下容易產(chǎn)生泄漏,造成齒輪泵漏油故障,可靠性差。
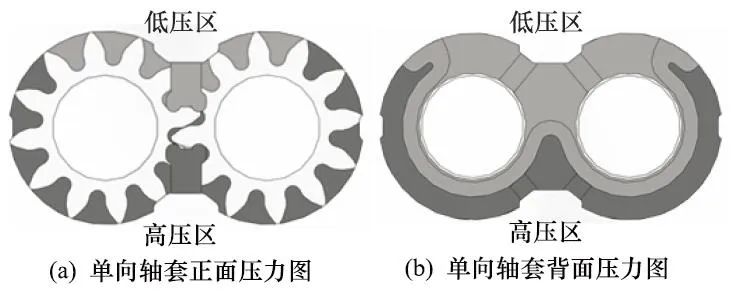
根據(jù)齒輪泵工作原理的幾何模型,抽取流體域作為流體仿真計(jì)算的區(qū)域,流體域共分成三部分:入口流域、泵內(nèi)齒輪傳動流域以及出口流域。大致可以得到如圖9所示的流線圖和壓力云圖。
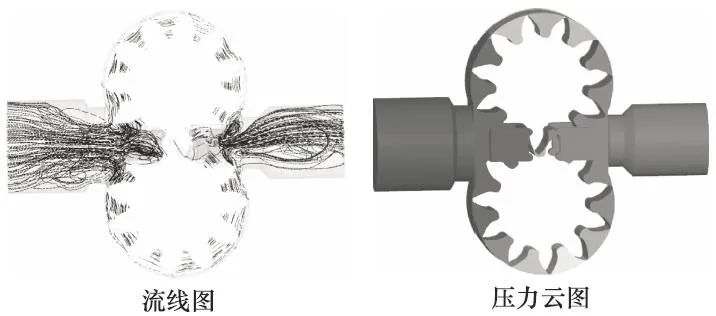
為了解決主動供油系統(tǒng)齒輪泵軸封的可靠性問題,采用一種雙向密封結(jié)構(gòu)方案,在軸套的背面將壓力區(qū)分為4個區(qū),低壓區(qū)、高壓區(qū)和2個次高壓區(qū)(見圖10),這種方案通過內(nèi)部異形密封圈將齒輪泵進(jìn)油腔道和旋轉(zhuǎn)密封腔道隔離,進(jìn)油腔道即使高壓也不會對旋轉(zhuǎn)密封腔造成影響,有效提高了旋轉(zhuǎn)密封的可靠性,同時(shí)通過縮小高壓區(qū)面積降低了浮動軸套的傾覆力矩,增加了軸套的平衡性能,降低齒輪徑向液壓不平衡力,改善齒輪和齒輪軸所受力情況。
2.2 增加泄油口解決高溫導(dǎo)致的油封唇口老化、油封失效問題
后蓋端增加泄漏油口結(jié)構(gòu)如圖11所示,充分利用產(chǎn)品內(nèi)部循環(huán)機(jī)構(gòu)的泄漏油對各重要摩擦副形成有效潤滑,由高壓區(qū)至低壓區(qū)產(chǎn)生的內(nèi)泄油液與泄油口的無壓力形成壓差,促使泄漏油的循環(huán)(如圖11中的循環(huán)回油腔道),從而通過外泄形式及時(shí)將各摩擦副產(chǎn)生的熱量充分散熱、排出,也確保了齒輪泵油封處的壓力和系統(tǒng)回油管路壓力一致,不超0.5MPa,油封唇口可靠性得到大幅提高。
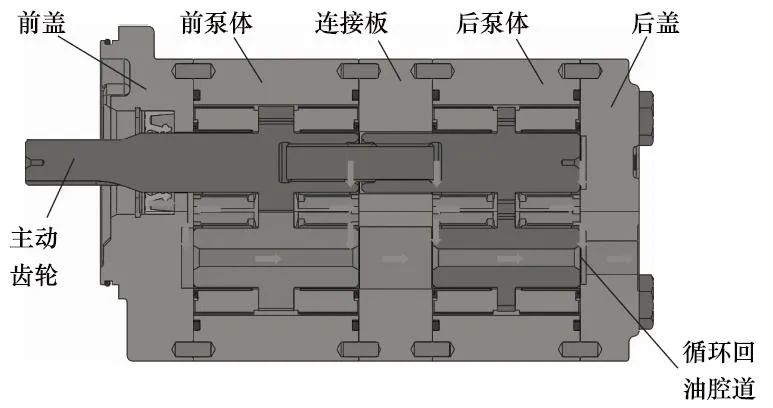
優(yōu)化后的主機(jī)主動供油系統(tǒng)工作原理如圖12所示。
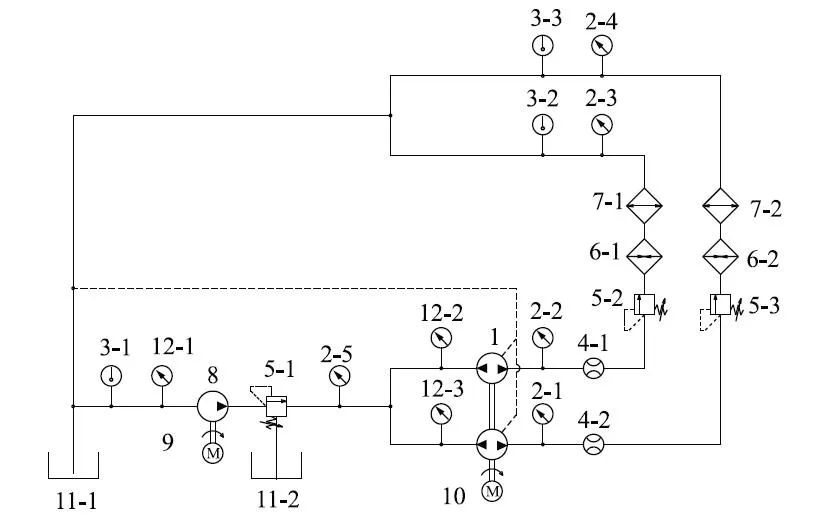
1.雙向結(jié)構(gòu)雙聯(lián)泵(小排量)3-1、3-2、3-3.溫度計(jì) 4-1、4-2.流量計(jì)5-1、5-2、5-3.溢流閥 6-1、6-2.加熱器 7-1、7-2.散熱器 8.増壓補(bǔ)油泵(大排量)11-1、11-2.油箱 12-1、12-2、12-3.真空表圖12 優(yōu)化后的主機(jī)主動供油系統(tǒng)工作原理
3.1 采用五段式結(jié)構(gòu)設(shè)計(jì),縮短雙聯(lián)泵總體長度提高整體剛度
整體結(jié)構(gòu)采用前蓋、前泵體、聯(lián)結(jié)板、后泵體、后蓋五段式結(jié)構(gòu)(如圖13)。更改常規(guī)產(chǎn)品(如圖14)的六段式雙連接板十字接頭連接方案(如圖15)為花鍵軸傳動單連接板(如圖16)形式,有效減小齒輪泵的軸向尺寸,提高功率傳輸?shù)目煽啃院头€(wěn)定性,切實(shí)提高了產(chǎn)品的功率密度水平。避免了如圖7所示十字接頭和連接扁鍵早期磨損故障的發(fā)生,提高了產(chǎn)品的承載能力和可靠性。
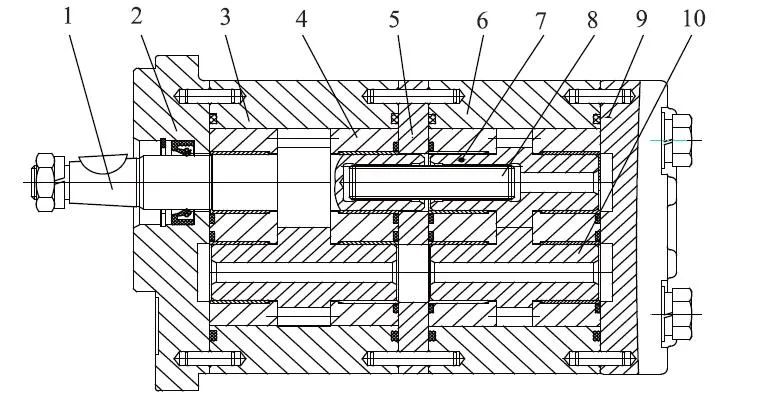
4.浮動軸套 5.聯(lián)結(jié)板 6.后泵體 7.后泵主動齒輪 8.花鍵軸 9.后蓋 10.從動齒輪(五段指2、3、5、6、9外形結(jié)構(gòu))
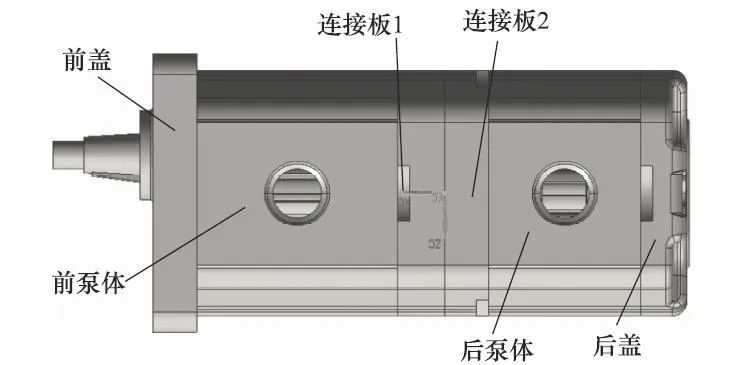
圖14 常規(guī)齒輪泵外形結(jié)構(gòu)
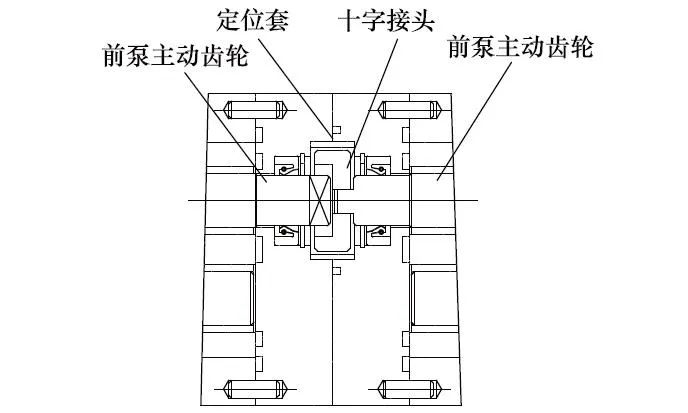
圖15 十字接頭雙連接板結(jié)構(gòu)圖
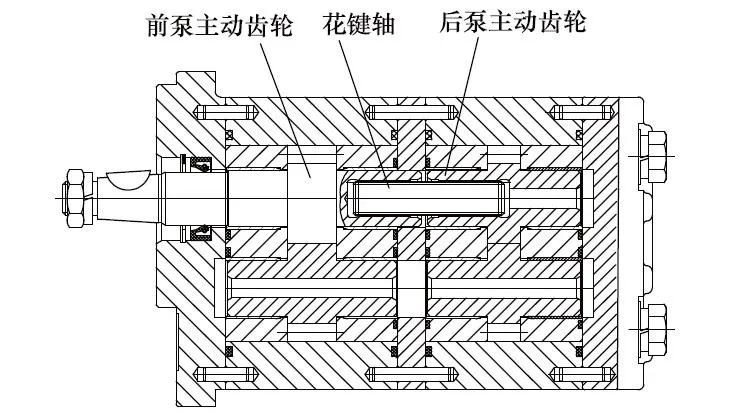
3.2 齒輪參數(shù)優(yōu)化設(shè)計(jì)[7]提高承載能力,解決產(chǎn)品高壓、高溫工況下容積效率低問題采用小模數(shù)多齒雙嚙合齒輪參數(shù)化設(shè)計(jì),并進(jìn)行三維仿真,模擬齒輪嚙合狀況,確定齒輪雙嚙合狀況最佳公法線工藝控制參數(shù)(見圖17),提高齒輪的承載能力。
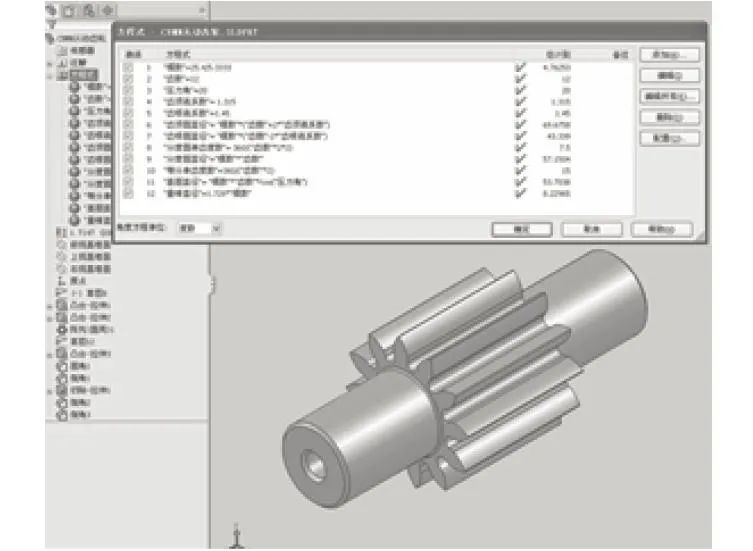
圖17 齒輪三維參數(shù)化設(shè)計(jì)齒輪軸頸采用大模數(shù)系列產(chǎn)品軸頸尺寸,有效提高齒輪軸頸的抗撓度變形,增加了低溫環(huán)境啟動扭矩性能。齒輪采用滾、剃齒形修形工藝優(yōu)化,改變齒輪齒面嚙合的應(yīng)力變形,有效降低齒輪嚙合噪聲(如圖18)[8]。
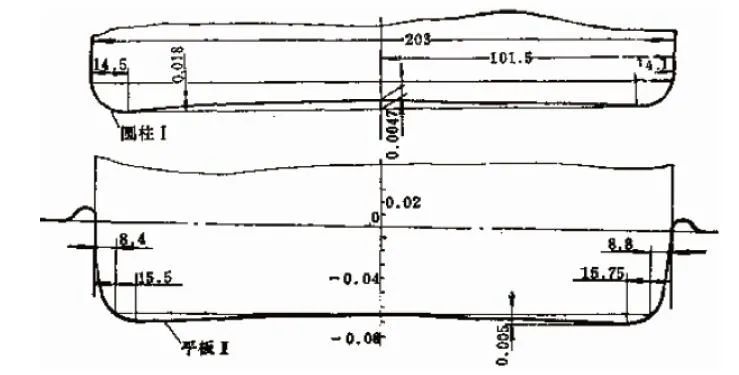
3.3 優(yōu)化浮動軸套高壓區(qū)設(shè)計(jì)提高產(chǎn)品軸向承載能力采用縮小高壓區(qū)雙向密封結(jié)構(gòu)(如圖8和圖10所示)。通過對單向和雙向密封結(jié)構(gòu)分析,設(shè)計(jì)的齒輪泵高壓、次高壓、低壓區(qū)域,有效降低齒輪承受的徑向液壓不平衡力。同時(shí)也減少了齒輪泵內(nèi)部高壓區(qū)面積,齒輪泵安裝螺栓承受高壓沖擊載荷狀況得到很好改善,增加了產(chǎn)品的整體剛度,避免出現(xiàn)螺栓斷裂故障(如圖5)。通過三維模擬齒輪雙面嚙合困油區(qū)間(如圖19),精確計(jì)算卸荷槽尺寸,優(yōu)化卸荷槽的高低溫、高速、高壓工況下的有效卸荷性能。
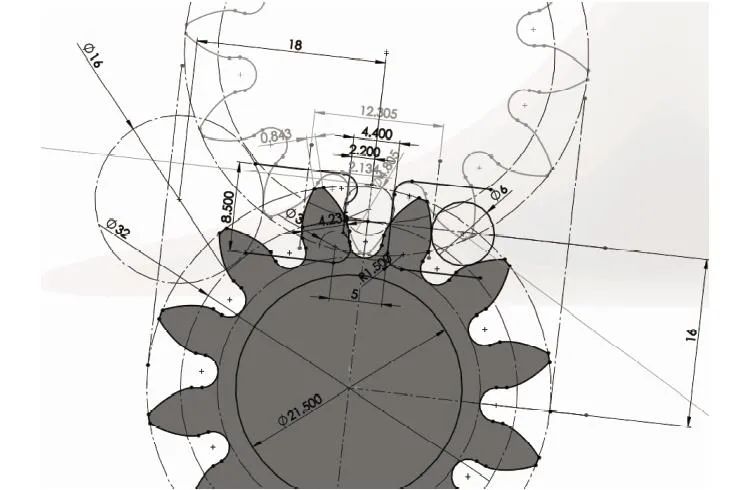
(1)采用氫化丁腈橡膠密封材料和PTFE組合油封結(jié)構(gòu)設(shè)計(jì)解決寬溫域工況密封有效性問題。
旋轉(zhuǎn)油封采用聚四氟乙烯特制油封以及特殊的唇口設(shè)計(jì)使產(chǎn)品滿足高轉(zhuǎn)速(4000r/min)以及低溫性能需求。氫化丁腈橡膠異形密封圈以及低塑性尼龍材料擋條組合式內(nèi)密封結(jié)構(gòu)滿足產(chǎn)品、正壓(2.5MPa)和寬溫域(-45℃~150℃)使用要求。(2) 內(nèi)部雙向浮動軸套密封結(jié)構(gòu)設(shè)計(jì)解決低溫高黏度啟動扭矩大以及高溫低黏度內(nèi)部泄漏大問題。對齒輪泵的間隙和內(nèi)泄漏方面的研究,國內(nèi)有很多。關(guān)于外嚙合齒輪泵內(nèi)泄漏理論模型的建立及參數(shù)優(yōu)化[9]均有所涉及。在低溫環(huán)境下,鋁合金泵體、浮動軸套和合金鋼齒輪由于材料特性不同,低溫環(huán)境下收縮率差異較大。隨著環(huán)境溫度降低,齒輪泵體內(nèi)壁與齒頂間間隙以及泵體厚度與齒輪厚度和浮動軸套厚度間形成的軸向間隙將逐步減小,在低溫運(yùn)行時(shí)齒輪旋轉(zhuǎn)切割鋁殼和軸套端面,不合適的間隙,造成泵體孔掃膛面以及軸套和齒輪間摩擦副面的破壞?;謴?fù)常溫后,齒輪泵的容積效率將大幅下降。通過大量的試驗(yàn)和仿真分析,我們發(fā)現(xiàn)在高溫時(shí),由于油液黏度的降低,齒輪泵的內(nèi)泄加大,但當(dāng)隨著溫度的升高,齒輪泵油液黏度下降有限,泄漏量總體變化不大。原因是高溫下, 油液黏度變小, 在不變的間隙下,泄漏已經(jīng)達(dá)到相應(yīng)的臨界值,幾乎接近泄漏的最大值,所以隨著溫度再增高,泄漏量變化不大。為了使產(chǎn)品具有低溫工況下的啟動低摩性,降低低溫下油液高黏度以及摩擦副間因間隙過小導(dǎo)致失效的可能性,減少產(chǎn)品高溫工況下泄漏量滿足產(chǎn)品高溫高效使用性能。結(jié)合小高壓區(qū)和雙向結(jié)構(gòu)設(shè)計(jì)思路,通過仿真和對比試驗(yàn)最終確定合理的徑向間隙和軸向間隙配合尺寸。并確定了三種壓力區(qū)間密封區(qū)域的分布和組合密封結(jié)構(gòu)內(nèi)部密封形式,提高了大軸向間隙配合下齒輪泵端面密封的有效性。具體密封結(jié)構(gòu)和區(qū)間劃分如圖20所示。
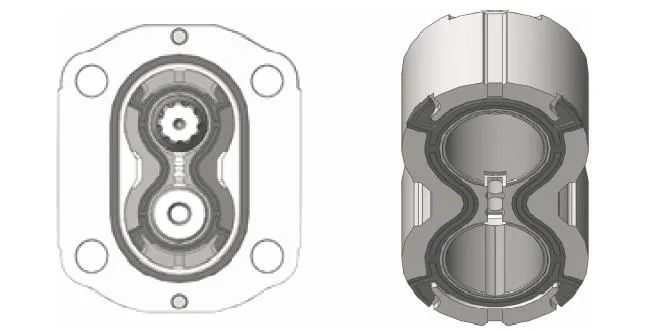
通過對主動供油系統(tǒng)工況以及齒輪泵內(nèi)部結(jié)構(gòu)的研究,綜合國內(nèi)外相關(guān)專業(yè)研究機(jī)構(gòu)對高流速導(dǎo)致氣穴現(xiàn)象發(fā)生以及高、 低溫液壓系統(tǒng)以及低摩材料方面的研究方案的綜合應(yīng)用。結(jié)合多年的齒輪泵生產(chǎn)和產(chǎn)品設(shè)計(jì)經(jīng)驗(yàn),本文很好地解決了齒輪泵的進(jìn)油正壓、高轉(zhuǎn)速、寬溫域以及高可靠性等方面性能需求問題。各項(xiàng)研究內(nèi)容也通過產(chǎn)品的實(shí)際應(yīng)用得到很好的驗(yàn)證。結(jié)合現(xiàn)階段綠色電動能源的高速發(fā)展也為齒輪泵向高轉(zhuǎn)速、寬溫域以及與變頻電機(jī)組合實(shí)現(xiàn)變流量控制方面的應(yīng)用提供了理論和方法支撐。